Factory and Warehouse
Product Form
Flanged Ductile Iron Steel Pipe Parameters:
Nominal Size (DN) | Outside Diameter [mm (in)] |
Nominal Wall Thickness [mm (in)] |
Flange Class | |
PN 20 | PN 35 | |||
100 | 122 (4.803) | - | 5.0 (0.197) | 7.0 |
150 | 177 (6.969) | - | 5.0 (0.197) | 8.0 |
200 | 232 (9.134) | - | 5.0 (0.197) | 8.0 |
225 | 259 (10.197) | 5.0 (0.197) | 5.2 (0.205) | 9.0 |
250 | 286 (11.260) | 5.0 (0.197) | 5.6 (0.220) | 9.0 |
300 | 345 (13.583) | 5.0 (0.197) | 6.3 (0.248) | 10.0 |
375 | 426 (16.772) | 5.1 (0.201) | 7.3 (0.287) | 10.0 |
450 | 507 (19.961) | 5.6 (0.220) | 8.3 (0.327) | 11.0 |
500 | 560 (22.047) | 6.0 (0.236) | 9.0 (0.354) | 12.0 |
600 | 667 (26.260) | 6.8 (0.268) | 10.3 (0.406) | 13.0 |
750 | 826 (32.520) | 7.9 (0.311) | 12.2 (0.480) | 15.0 |
Introduction
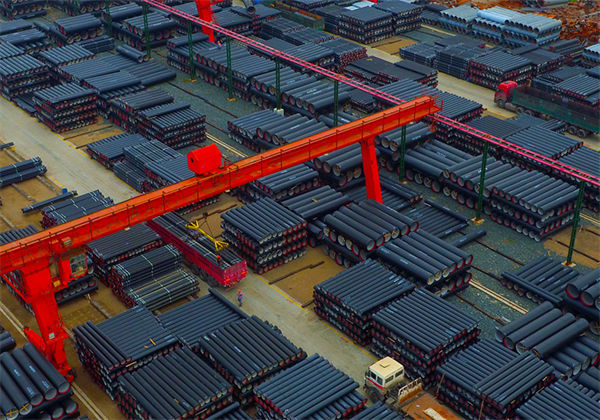
Flanged Ductile Iron Pipe, an exceptional piping solution designed to cater to a wide range of industrial and municipal applications. This high-quality ductile iron flanged pipe offers superior strength, reliability, and versatility, making it an ideal choice for various fluid transportation systems. With its double flanged design, our product ensures easy installation and connection, providing a seamless and efficient flow of fluids for your projects.
Key Features:
Durable Construction: Our Flanged Ductile Iron Pipe is manufactured using top-grade materials, ensuring excellent durability and resistance to corrosion and external impacts. This longevity extends the pipe's service life and significantly reduces maintenance costs.
High Strength: The ductile iron material used in our pipes provides impressive mechanical properties, offering enhanced strength and toughness. This feature makes our product suitable for both underground and above-ground applications, guaranteeing reliable performance in challenging environments.
Versatile Applications: Whether it's water supply, sewage systems, irrigation, or industrial fluid transportation, our Flanged Ductile Iron Pipe adapts to various applications with ease. Its compatibility with different media and temperatures ensures efficient and safe fluid transfer.
Easy Installation: The double flanged design allows for convenient and secure connections, saving time during installation. The flanges also provide flexibility for alignment adjustments, ensuring a perfect fit with other pipeline components.
Low Friction Loss: The smooth internal surface of our ductile iron pipe minimizes friction loss, enabling efficient flow rates and reducing energy consumption, making it a cost-effective solution for long-term projects.
Environmentally Friendly: Our Flanged Ductile Iron Pipe is an eco-conscious choice, as it is 100% recyclable and contributes to sustainable waste management practices.
Applications:
Water Distribution Systems: Municipal water supply and distribution networks benefit from the high strength and corrosion resistance of our ductile iron flanged pipe.
Sewage and Wastewater Management: The pipe's robust construction ensures reliable conveyance of sewage and wastewater.
Industrial Applications: From chemical processing to mining operations, our pipe provides a safe and dependable fluid transportation solution.
Irrigation Systems: Agricultural projects rely on our Flanged Ductile Iron Pipe to ensure efficient irrigation and water distribution.
Conclusion:
In summary, our Flanged Ductile Iron Pipe is a reliable, durable, and versatile solution for a wide range of fluid transportation needs. Its double flanged design streamlines installation and connection processes, while its superior strength and low friction loss make it a cost-effective choice for long-term projects.
Benefits of ductile iron pipe
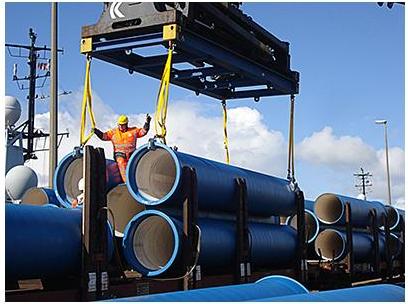
Solid under loads
In underground conditions, the ductile cast iron pipe has a semi-rigid behaviour: it offers an excellent compromise between mechanical stress in the wall (small DN) and ovality (large DN). It can be laid in high and low height of cover, and easily in soil of low rigidity. The ”ground/semi-rigid pipe” system offers optimum mechanical stability over time, without risk of buckling in large DN.
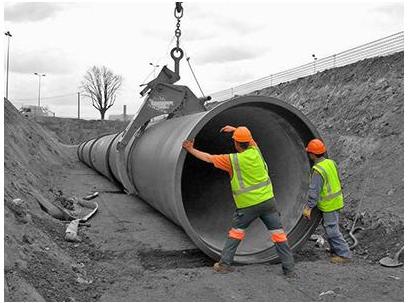
Insensitive impacts
The ductile cast iron structure has a high elastic deformability and a high resistance to crack initiation: it results in excellent impact resistance. The cast iron pipes are perfectly suited to transport conditions over long distances (truck, train or ship), handling conditions on sites and to different types of backfilling. The ductile cast iron pipelines may be laid in very difficult areas: rocky mountain slopes for hydroelectric plants, crossings for cantilever bridges, rockfill for submarine outlets.
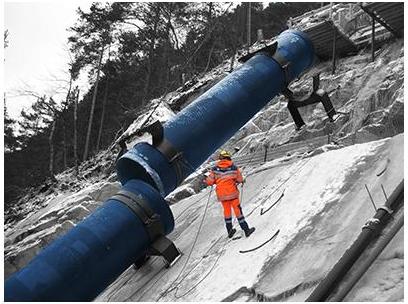
Push-in joint system
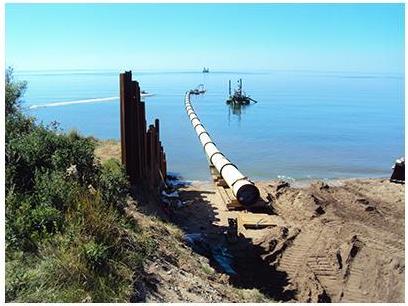
Excellent hydraulicity
The centrifugation process ensures a perfectly smooth and even cement surface. The Colebrook roughness coefficient of an isolated pipe is k = 0.03 mm. We recommends the use of an average value of k = 0.1 mm for sizing networks in order to take into account all the different load losses caused by singular points (tee fittings, elbows, valves, etc.)
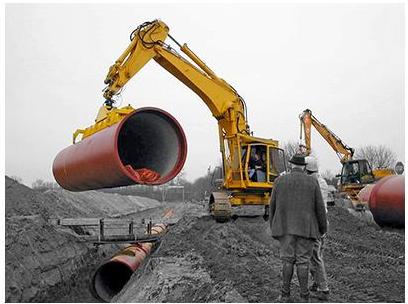
Pressure resistance
The ductile cast iron pipe are designed to withstand pressures much greater than the values usually encountered on the networks. The wall thickness is calculated with a safety factor of 3 with respect to the maximum operating pressure. This additional safety margin is very useful to the impacts during installation, accidental overpressure and mechanical operating fatigue.